3D Digital Fabrication
-
Providing digital fabrication tools that transform imagination into reality
Outline of 3D Digital Fabrication Business
The mission of 3D Digital Fabrication Business has been to provide easy-to-use digital fabrication tools to enable everyone with the capability of transforming their imagination into reality. In keeping with its concept of desktop fabrication, DGSHAPE develops a range of digital tools that are compact in size, easy-to-use and affordable. DGSHAPE’s truly innovative product range includes 3D milling machines and 3D printers as well as engraving machines and photo impact printers that are developed with proprietary technologies and are held in the highest regard by creative individuals worldwide. Products are designed to suit a wide range of applications, from creating prototypes in product design and development to education and research for training upcoming designers and engineers, as well as engraving and other professional creative arts, right down to individual hobbyists.
-
3D Milling Machines
3D milling machines are used in the manufacturing industry for product design and prototyping, rapid manufacturing and jig fabrication, as well as in high schools and university labs for education and research. Models are available for working with a broad range of materials from resins, such as chemical woods, to aluminum and brass, and offer high-speed, high-precision operation in a compact size. Milling machines come equipped as standard with DGSHAPE’s proprietary CAM software for applications tailored to a wide range of 2D and 3D milling processes.
Applications
-
Product Prototypes -
Structural Design Evaluation -
Jig and Part Production
-
3D Printers
Incorporating a stereo-lithography process using a UV-LED projection system, the additive rapid prototyping machine builds models by sequentially curing layers of resin from a liquid resin vat. While subtractive machines provide outstanding accuracy and smooth finished surfaces for applications that require a precise level of machining, additive machines are suitable for quickly checking a design in the initial stages of prototyping or modeling a complex shape. DGSHAPE offers a proprietary combination solution that delivers the merits of both types of machines, so that users can select the best method to suit the requirements or conditions in each step of their workflow, from inspiration to production.
The UV lamp instantly cures and laminates acrylic resin to build 3D shapes.
Applications
-
Design Prototypes -
Product Prototypes -
Industrial Part Prototypes
-
Engraving Machines
Engraving machines can be used to carve text and unique designs on a wide range of materials, including plastic, acrylic, aluminum, stainless steel, brass and wood. They are used for making signs and nameplates, as well as engraving text, logos and other graphics into accessories, gifts and awards.
Applications
-
Signs -
Personalized Products -
Name and Product Plates
-
Photo Impact Printers
The desktop photo impact printer strikes surfaces including metals and resins with a precision diamond-tipped stylus, reproducing text, logos and other graphics at high speed and with pin-sharp accuracy. The size and density of impact dots can be changed to create stunning illustrations and smooth photo gradations. Photo impact printers are used in a diverse range of applications such as imprinting names and decorations onto custom accessories and gifts, and are also ideally suited for industrial marking applications, including the production of serial number and information plates.
Applications
-
Personalized Gifts -
Stationery -
Serial Number Plates
3D Digital Fabrication Business Strategy
Roland DG was established in 1981 during a period characterized by tremendous interest in personal computers. As computers began to revolutionize society and industry, Roland DG envisioned computer peripherals that would work as “digital hands” to facilitate a world where everyone could enjoy their individual creative pursuits and transform their imagination into reality. The concept of desktop fabrication, focused on providing compact, affordable, and easy-to-use value, was born from this vision.
In 1986, Roland DG released the world’s first desktop 3D milling machine, the CAMM-3 PNC-3000. The PNC-3000 enabled engineers and designers to observe for the first time materials being fabricated on their desktop next to a personal computer. This process, dubbed the “magic hand,” radically streamlined the rapid prototyping and design process, and created the means for anyone with a personal computer to undertake desktop fabrication.
It has now been three decades since Roland DG released its personal 3D milling machines, and the concept of desktop fabrication continues to draw a growing level of interest every year. The growth of the internet and social media, the availability of smart devices and personal-use 3D printers, and the increase in the number of public workshops such as Fab Labs and manufacturer studios has expanded the horizons of digital creation among a vast number of people globally. There is no doubt that we’re entering an age where anyone with an idea has the potential to become a “Maker.” Fabrication is no longer an art that is limited to manufacturing companies, R&D departments or specialists, but instead has expanded beyond traditional workplaces, fields of specialties and corporate or industrial divisions, as well as cultures and values, and has the potential to create new, innovative applications from the collective knowledge and ideas of people around the world.
With such significant advances occurring globally throughout a variety of digital fabrication fields, DGSHAPE will focus its research and development at providing further innovation and value to customer fabrication efforts. While maintaining its position in its core markets, DGSHAPE will also focus on harnessing next-generation technologies like IoT, AI and robotics to develop solutions suited to a new era of creativity and fabrication. Just as Roland DG previously identified and generated new business growth from its 3D digital fabrication technologies, DGSHAPE will continue to identify and explore the seeds of new businesses opportunities for future growth.
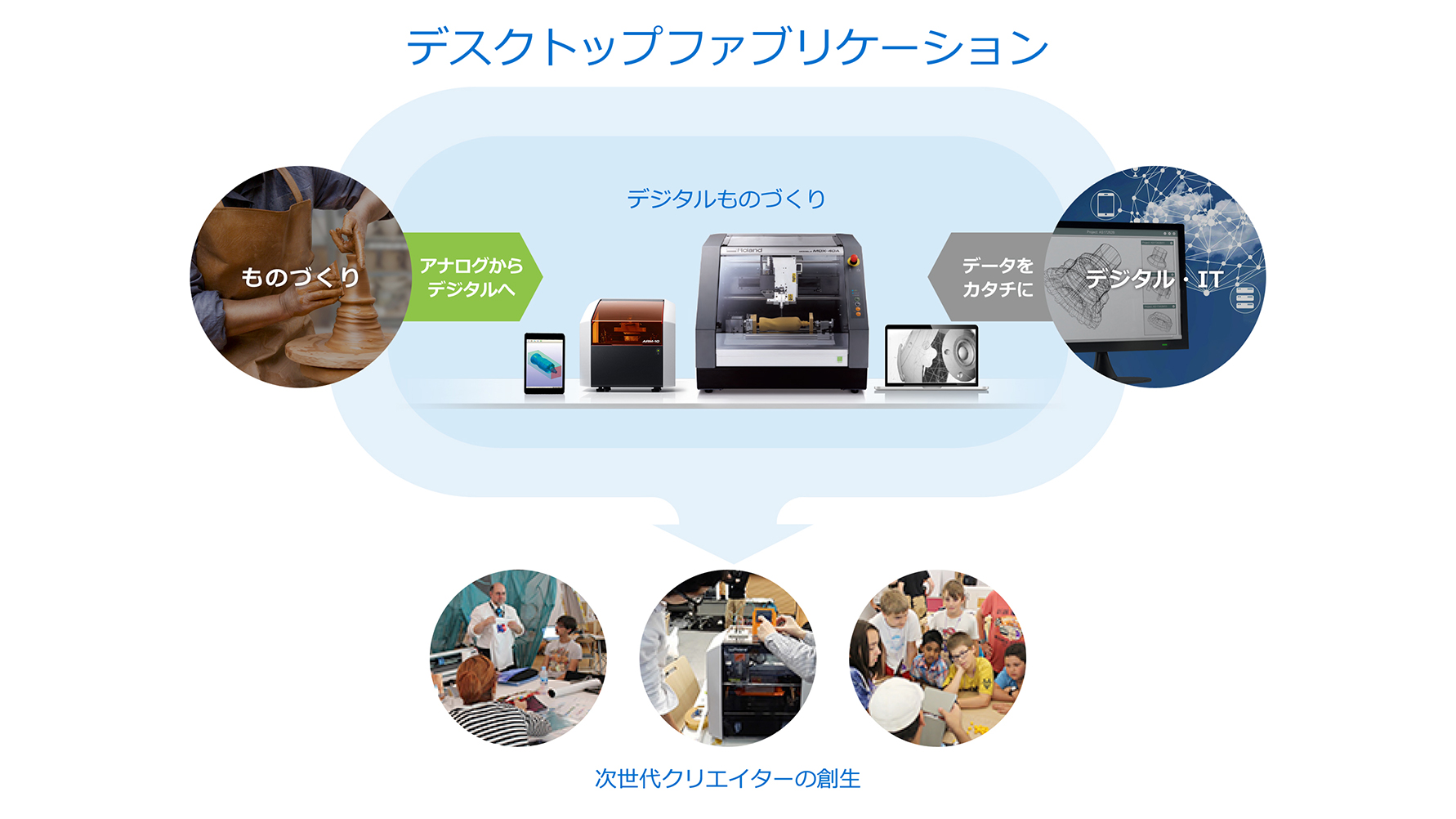